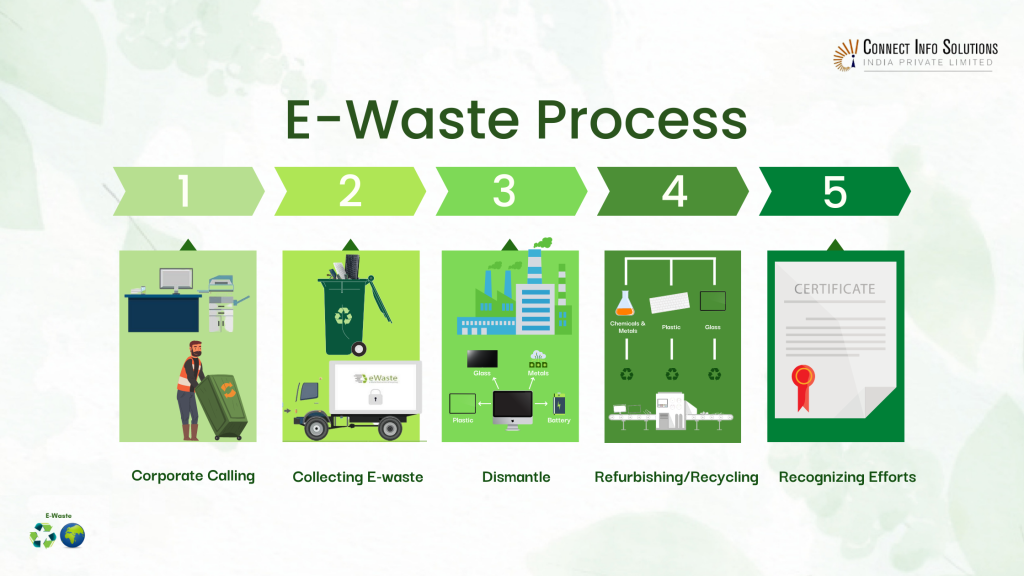
Introduction
India lacks valuable mineral reserves, and undiagnosed e-waste ends up in landfills. Therefore, a well-designed, monitored e-waste healing system that generates wealth and employment is required. Desktop computers, chipsets, cell phones and power strips, floppy disks, headsets, tv sets, coolers, and fridges are all examples of electronic waste (e-waste).
According to the study, one compactor in China now generates more cobalt (via recycling) than the nation’s mining areas within a year. In addition, materials melted down from reprocessed ore are 2 to 10 times more fuel efficient than metallic materials from virgin ore.
E-Waste Management: A Silent Menace
As reported by the Global E-Waste Monitor 2017, India produces approximately 2 million tonnes (MT) of e-waste per year, ranking fifth among e-waste-growing regions after the United States, China, Japan, and Germany. However, the handlers took care of just 0.036 MT of India’s e-waste in 2016-17.
Approximately reprocessing 95% of India’s e-waste happens in the underground economy and is inefficient. According to a review on e-waste introduced by the United Nations (UN) at The World Economic Forum on Jan 24, 2019, the garbage attained 48.5 MT in 2018. It will continue to double unless anything alters.
Since 2011, India has enacted legislation to handle e-waste, requiring only authorized wreckers and refiners to obtain e-waste. On Oct 1, 2017, the E-waste (Management) Regulations, 2016 were implemented. The law’s scope covered over 21 goods (Schedule-I).
The Procedure For Handling E-Waste
Step 1: Collecting and transporting
- The very first step in reprocessing e-waste would be this. Refiners set up take-back counters or gathering containers in these locations.
- The recycling facilities then transfer the e-waste to recycling centres and amenities after these containers are full.
Step 2: Grouping and Slashing
- The process of sorting and shredding electronic waste comes after collection and transportation. Shredding is crucial to the achievement of any successive detachment. Effectiveness is essential at this point because of this.
- Inappropriate processing, e-waste must be broken down into smaller fragments through shredding. These microscopic prices are individually arranged before being disassembled. Usually, this requires a lot of labour because waste is currently being detached into its constituent elements.
- Materials are then divided into core components and secondary materials. These items are subsequently categorized after being sorted. These products fall into two categories: those that can be recycled further and those that consumers can use immediately.
- E-waste is typically mechanically sequenced, but materials like artificial light, battery packs, UPS batteries, and toners shouldn’t be squashed or ripped up individually.
Step 3: Dust Removal
- Through a procedure of shaking, the minute refuse fragments are evenly distributed on the conveyor.
- The evenly dispersed e-waste pieces are then broken even more. The dust is derived and adequately disposed of without damaging the environment. This strategy prevents environmental deterioration.
Step 4: Magnetic Separation
- After that, a powerful overhead magnet aids in separating disposal materials containing steel and iron. In this manner, the steel from the solid waste has been effectively reprocessed.
- A few mechanical processes might occasionally be necessary to distinguish circuit, copper, and aluminium from several other suspended particles.
Step 5: Water Separation
- Water separation technology is then used to distinguish the glass from the polycarbonate.
- Handlers can then deliver glass-containing plugs to blast furnaces for use in creating new CRTs, x-ray pipes, and battery packs.
Step 6: Waste stream purification
- The next step is to find and remove lingering metals from plastics to decontaminate the wastewater further.
Step 7: Getting Recycled Materials Ready for Selling
- The preparation of recycled content for selling is the last step.
- Here, the SSS-separated materials are ready to be sold as raw materials for producing electronic gear.
International Contribution of E-Waste
More optimistically, news reports stated that the awards for the 2020 Tokyo Olympics used 50,000 tonnes of e-waste. The steering group made all prizes from old devices, computers, and other electric devices. Organizers had collected 47,488 tonnes of gadgets by Nov 2018, of which they will obtain approximately 8 tonnes of gold, silver, and bronze to create 5,000 medals. In Japan, about 1,600 governmental officials, or 90%, were implicated in processes. Furthermore,
Since 2015, the Department of Electronics and Information Technology (MeitY) has collaborated with professional organizations to launch an e-waste education campaign under Digital India to teach the general public about the risks of unorganized e-waste composting. To enlighten them about alternative ways of getting rid of their e-waste.
The initiative emphasizes the importance of environmentally friendly e-waste safe disposal. The initiative has embraced the greatest e-waste responsible practices available internationally to ensure that this industry can increase employment in addition to attractive investment opportunities for residents.
Collection and Recycling Technology Development
The MeitY has established innovative products to reuse valuable metals and polymers sustainably, including two unique PCB technologies with appropriate regulatory protections, 1000 kg/day (35 MT e-waste) and 100kg/batch (3.5MT e-waste). The 1000kg PCB/day continuous quality factory would’ve been appropriate for establishing a countrywide eco-park, while the 100kg PCB/batch production process would’ve been appropriate for the underground economy. It is attainable by improving and converting the current situation in the shadow economy.
There is an increased opportunity to increase e-waste composting in the nation. There have been a few steps forward in this path; nevertheless, much more surfaces must be protected through community outreach, training programs, labour productivity, and technology adoption, all while implementing sufficient safeguards in the nation’s informal economy. Given India’s scarcity of valuable metal ores, the nation requires a well-designed, reliable, and controlled e-waste healing rule to create wealth and employment.
The Bottom line
Seeing this elevated amount of e-waste generation in India, the government and big industries must take serious steps to treat them most effectively. There is a massive need to deal with this e-waste in an environmentally feasible way to help the soil and underground water maintain their natural nourishing properties. This post is an eye-opener for everyone uninformed and ignorant about reality.
What do you think is your responsibility towards the environment? We are happy to discuss all the possibilities of responsibly disposing of your e-waste. Let’s connect on